Predictive maintenance is an ice-breaker when it comes to increasing operational efficiency at your factory or industry. In the highly competitive age that we live in today, industries are increasingly resorting to predictive maintenance for reducing the downtime of their machines and equipment. Let’s figure out, how Predictive Maintenance using IoT is helping industries.
Companies are utilizing the Internet of things (IoT)-based technologies to create easily deployable comprehensive predictive maintenance solution packages at an affordable budget. As per a report by ARC, predictive maintenance has emerged to be the largest domain where IoT is finding applications in all sectors.
In this article, we shall focus on the evolving trends in IoT-based predictive maintenance
THE PREDECESSORS: REACTIVE MAINTENANCE AND PREVENTIVE MAINTENANCE
Today factories mainly follow what is known as Run-to-Failure maintenance and Preventive Maintenance models for the upkeep of their machines and equipment.
The reactive model of maintenance is one where equipment is maintained or replaced only when it is rendered useless due to a failure. A reactive model is highly inefficient and leads to lower machine availability and higher downtime. It is due to this reason that the reactive model is best-suited for those less-critical assets in the operational process whose unavailability has little impact on production.
On the contrary, a preventive maintenance model is where teams in charge of maintenance carry out repair and replacement jobs on machines based on a predefined maintenance schedule.
More often than not, these schedules are prepared in accordance with the manufacturer’s terms of use. While preventive maintenance reduces machine downtime more effectively compared to reactive maintenance, its maintenance schedules can often not be in consonance with the actual operating conditions. This may hamper machine operation as well as raise maintenance costs.
Both these approaches do not assess or predict the actual working condition of machines.
WHAT IS PREDICTIVE MAINTENANCE?
At the core of it, predictive maintenance is about using smart technology like IoT to take care of all the machines present before they start to break down. So, instead of just fixing equipment on a scheduled date, it closely checks the machine health in real time. Upon finding any signs of trouble, the system immediately notifies you so that the problem is fixed before it becomes too serious to handle. The benefits? You will avoid sudden breakdowns, save a lot on costly repairs and have everything running smoothly. Certainly, predictive maintenance using IoT help businesses continue working more efficiently than ever without any unexpected delays.
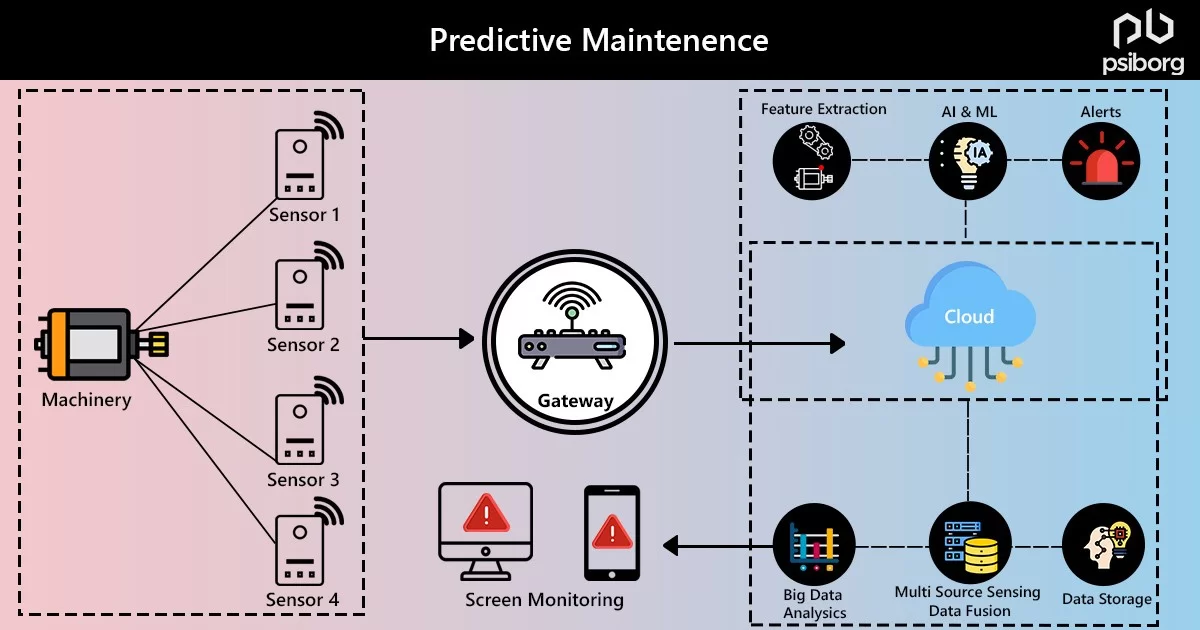
Suggested Reading: SMART IOT SOLUTION
PREDICTIVE MAINTENANCE IN IOT
The idea of predictive maintenance is based on knowing and understanding the running condition of the machine. Knowledge about the running condition of the machine can lead to better maintenance and machine reliability. To know and understand machine health, various parameters such as vibration, the temperature of the machine, etc can be used.
These parameters can be continuously monitored with the help of sensors that can be installed at various places on the machine. Analyzing the output of these sensors through suitable software can help in effectively understanding machine health. Although this method of maintenance is highly effective, it is quite expensive.
TRENDS IN IOT AND OTHER TECHNOLOGIES- THE ROAD TO MAINSTREAMING OF PREDICTIVE MAINTENANCE
Thanks to the Internet of things (IoT), the idea of predictive maintenance is gaining traction. With IoT, continuous monitoring of machines and machine parts is becoming a reality. The use of wireless sensors that can talk to each other has made predictive maintenance with IoT affordable to companies. Among the many technologies that are powering this revolution in IoT-based predictive maintenance are:
WIRELESS TECHNOLOGIES USED IN IOT
As the IT revolution surges, the speed and quality of wireless technology are getting better each day. Take Wi-Fi technology or 4G internet speeds for that matter. With such excellent connectivity, wireless sensors can easily transmit and receive machine health data. Also, there are Low Power Wide Area Network technologies, like LoRaWAN, Zigbee, BLE Mesh etc which are used when a large number of sensor devices send data to the central Unit. This has not only made monitoring of machine health automatic but also more accurate and cheaper.
LOW-COST SENSORS USED IN INDUSTRIES
With the rapid penetration of smartphones across the world, the smartphone industry has grown by leaps and bounds. The growth of the smartphone industry, on the other hand, has been putting downward pressure on the price of sensors. These miniaturized smart sensors are just what the doctor ordered for the IoT-based predictive maintenance technology. There are sensors like humidity sensors and temperature sensors that are widely used in IoT.
CLOUD COMPUTING AND EDGE COMPUTING IN IOT
The advances in cloud computing have made data transfers, storage, etc quite inexpensive and secure. IoT Cloud computing platforms such as AWS are increasingly being used by companies for their IoT and related computing needs. This has opened a world of possibilities for predictive maintenance through IoT. Edge computing is widely used in IoT Edge gateway and now has become an integral part of IoT. Cloud and edge computing differ as Edge computing is the act of running workloads on edge devices; While Cloud computing is the act of running workloads within the cloud.
PREDICTIVE MAINTENANCE WITH ARTIFICIAL INTELLIGENCE AND MACHINE LEARNING (AI/ML)
Artificial Intelligence can be a powerful tool to help analysts analyze sensor data to continuously monitor and understand machine health, and carry out predictive maintenance. Machine Learning is the subset of Artificial intelligence, that can acquire knowledge and learn by itself based on algorithms. AI and ML with IoT together have very high potential.
FUTURE OF PREDICTIVE MAINTENANCE USING IOT
Factories are responsible for churning out goods that make our lives more convenient and pleasurable to live. Whether it is the AC that cools our homes or the cars that we drive, everything is made in factories. IoT-based predictive maintenance has the potential to further raise the efficiency of our industrial processes leading to greater operational efficiency, better supply chain and inventory management, and lower costs.
Hence, there’s no reason for industries to wait any longer to adopt the idea of IoT based predictive maintenance.
Also Read: M2M COMMUNICATION AND CONNECTED DEVICES and WHAT IS IOT PREDICTIVE MAINTENANCE? AND HOW IT WORKS?
PsiBorg is an IoT solution Provider, where we have developed various solutions for different industries including predictive maintenance.
FAQs
It’s actually the use of sensors, data analytics and IoT to monitor how the machines are working and predict potential failures a lot before they happen and give a hard time. This really helps businesses avoid any unexpected damage and, of course, unnecessary servicing.
The three common types of predictive maintenance using IoT are vibration analysis (which detects mechanical issues), thermography (for identifying overheating parts) and oil analysis (which monitors breakdown). These really help with live monitoring of the machines/equipment and making better decisions.
In preventive maintenance, there’ a fixed schedule to be followed even if the machine is working just fine. However, predictive maintenance sees machine health in real time to decide if and when it needs servicing. Hence, the predictive method is much more efficient and cost saving.
The many advantages of predictive maintenance include reduction in unexpected downtime, lower maintenance costs, higher equipment life and overall safety at work. Predictive maintenance using IoT goes a step ahead and provides real-time insights so that managers can take quicker and more accurate decisions.